Effect of Metal Impurities on Potassium Chloride Zinc Plating
Dec 25,2020
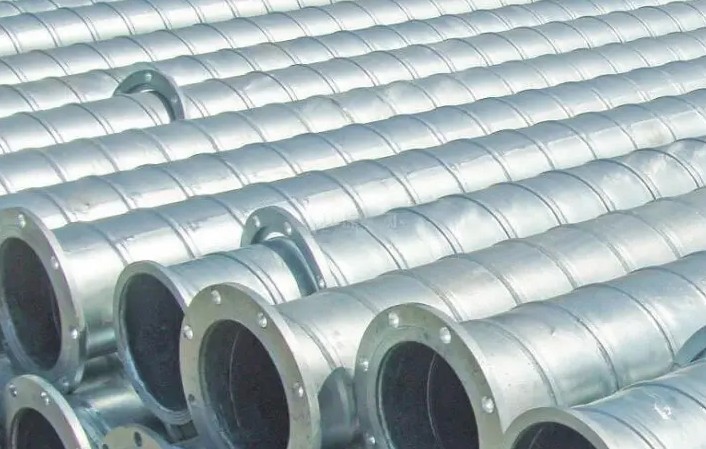
Metal impurities often pose a great danger to the electroplating working solution. Acid potassium chloride zinc plating is most often affected by iron impurities, followed by copper, lead and other metal impurities are also harmful.
Effect of Iron Impurities There are two types of iron impurities present in the bath, one is divalent iron and the other is trivalent iron. The allowable concentration of trivalent iron is high, and the plating solution can still work normally when it reaches 10g/L. Bivalent iron is more sensitive, will make the current density range significantly reduced, especially affect the quality of high current density area coating. In the Hull cell test, it was found that when divalent iron was added to 0.2g/L, scorched and rough areas appeared at the high current end for nearly 20mm. When added to 0.3g/L, scorched and rough areas appeared at almost half of the samples, and the coating in the low current area was ash. If this plating solution is used for barrel plating, the plating layer close to the roller wall will be severely burnt, which is the black spot, commonly known as roller printing. Iron ion pollution will be caused by improper treatment before plating, plating parts falling into the plating tank and not being fished out in time, chemical dissolution due to reaction with plating solution, etc. Excessive iron ions are usually treated with hydrogen peroxide and then filtered. Hydrogen peroxide is recommended to be added after dilution.
Copper impurities below 10mg/L have little effect on the zinc coating. However, with the increase of copper impurity content, the influence will also increase. When 0.15g/L is reached, the coating in the high current density area will appear obvious scorching and roughness, the coating in the low current area will turn black, and the coating with 3% dilute nitric acid volume fraction will be less bright than that in the absence of light. A small amount of copper impurities can be electrolytically treated at a low current density of 0.1 to 0.15A/dm2, and the length of treatment depends on the amount of copper content. In electrolytic treatment, the cathode is preferably corrugated iron plate.
In the case of more serious coating blackening and tight time requirements, it can be treated with zinc powder. The amount of zinc powder is about 2g/L. Copper impurities are mainly to prevent copper rods, anode copper hooks and hangers from falling into the plating tank, and to prevent patina from falling into the plating solution. Lead impurities are usually not encountered, if there are lead impurities, the first should be checked is the zinc plate. If it is a new plating solution, it is necessary to consider the quality of zinc chloride.
The influence of lead impurities is even more serious than that of copper impurities. In the light, the coating fogs after passivation, and the passivation film changes color quickly. In the heavy case, the coating does not deposit during barrel plating. It seems that there is a coating, but once dilute nitric acid emits light, it will soon be exposed. The content of lead impurities should be controlled below 5mg/L. Lead impurities can be treated by electrolysis or zinc powder, but it is more difficult to handle than copper. Lead impurities contaminated zinc plating solution, such as white passivation after plating, it is difficult to get blue-white film; because lead mainly from poor quality zinc plate, so first of all to check whether there is a problem with the zinc plate.
Contact Us
E-mail:
sales@dazhichem.com
Phone/WeChat:
+86-18520125168
Address:
No.1 Tianyuan East Road, Yonghe Economic Zone, Huangpu District, Guangzhou City